-
- News
- Books
Featured Books
- pcb007 Magazine
Latest Issues
Current IssueAlternate Metallization Processes
Traditional electroless copper and electroless copper immersion gold have been primary PCB plating methods for decades. But alternative plating metals and processes have been introduced over the past few years as miniaturization and advanced packaging continue to develop.
Technology Roadmaps
In this issue of PCB007 Magazine, we discuss technology roadmaps and what they mean for our businesses, providing context to the all-important question: What is my company’s technology roadmap?
Wet Process Control
In this issue, we examine wet processes and how to obtain a better degree of control that allows usable data to guide our decisions and produce consistently higher-quality products.
- Articles
- Columns
Search Console
- Links
- Media kit
||| MENU - pcb007 Magazine
Estimated reading time: 10 minutes
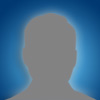
Contact Columnist Form
What's Your PCB Assembly IQ? - Corrosion Happens by Marissa Oskarsen
Corrosion of printed circuit assemblies happens--and it’s going to happen more and more as components get smaller and operating environments become more harsh. Tight spacing between conductors, residues of aggressive fluxes, and high heat and humidity can combine to become the perfect storm for creating corrosion-related field failures.
Do you know what causes, and prevents, PCBA corrosion? Take this 10-question quiz to determine your corrosion IQ.
Questions, Part 1: Multiple Choice
1. Which of the following is not a form of corrosion? a. Electrochemical migrationb. CAFc. Solder drossd. Dendritic growth e. Creep corrosion (Hint: Don’t pick this answer!)f. None of the above 2. What causes corrosion? a. Operating environments b. Halides – mainly bromides, chlorides, sulfides and fluoridesc. Halide-free PCB fab and/or assembly chemical residues d. All of the abovee. None of the above
3. How does corrosion affect electronic assembly performance?a. Creates no operational interferenceb. Causes intermittent functionality problemsc. Completely disables electronic assembliesd. Any of the above e. None of the above
Questions, Part 2: True or False?
4. Most analytical labs can provide root causes analysis for corrosion. 5. Residual PCB fabrication and assembly chemicals are rarely the root causes of corrosion. 6. IPC standards dictate cleanliness levels for PCB fabrications and assemblies. 7. Proper cleaning will prevent many forms of electrochemical corrosion.8. Conformal coating will help prevent environmental corrosion.
Questions, Part 3: Multiple Choice
9. What are the best conformal coatings to ward off corrosion? a. Urethanesb. Silicones c. Acrylicsd. Epoxies e. Parylene10. How can you ensure conformal coatings completely cover the desired area?
a. Visual inspection with 10X ring light or Luxolamp b. Immersion testc. UV inspection d. Automated optical inspection (AOI) e. None of the above
Answers1. Correct answer: C, solder dross. Solder dross is the fluffy-looking grey stuff that floats on top of solder pots. It’s mostly tin oxide and is not a product of corrosion.
Cheryl Tulkoff, senior member of DfR Solutions Technical Staff and internationally-recognized reliability expert, helps identify the different forms of corrosion and provided really cool photos.
Electro-chemical migration (ECM) is a specific type of corrosion caused by the movement of metal ions through an electrolytic solution under an applied electric field between insulated conductors. It is found on die surfaces, epoxy encapsulants, PCBs, and passive components (Figure 1).
Figure 1: Electrochemcial migration (ECM) on ceramic chip.
CAF or Conductive Anodic Filament formation is a form of corrosion inside the PCB (Figure 2).
Figure 2: Conductive anodic filament (CAF).
Dendritic growth is corrosion that grows beautiful fern-like fronds that short across conductors (Figure 3).
Figure 3: Dendrite bridging two PCB traces.
Creep corrosion makes your circuit boards look like chia pets as the copper sulfide creeps across their surfaces (Figure 4).
Figure 4: Creep corrosion.2. Correct answer: d, all of the above. Harsh operating environments like corrosive gasses, salt atmospheres, or high heat and humidity can contribute to corrosion. Halides are often cited as causes of corrosion, so many OEMs and CEMs try to avoid them in their flux formulations. But it turns out that fluxes that don’t contain halides have also been cited as root causes. What’s up with that? To make matters worse, it turns out that while our industry seems to focus exclusively on ionic contaminants, non-ionics can cause failures as well! Tulkoff cites polyglycols as an example: When present they turn surfaces from hydrophobic (water repelling) to hydrophilic (water attracting). These compounds are not ionic and they fly under the radar of conventional contamination tests. Is nothing considered “safe” anymore?3. Correct answer, d: any of the above. When it starts, corrosion might not present any functional issues to the PCB. That’s the stage where it hasn’t destroyed much of the circuitry yet. Yet. As it grows, it may cause intermittent opens or shorts, and as down hole tool expert Bill Parks points out, it will eventually kill the PCB completely, with no chance of repair.4. Correct answer: False. While most labs do have super-fancy analytical machines that can identify chemical elements and compounds associated with the corrosion, not all of them know enough about PCB assemblies and processes to help identify the root cause. Remember the movie My Cousin Vinnie? The dweebie lab guy knew all about the rubber he scraped from a set of tire tracks, but not enough about cars to know the vehicle that burned the rubber in the first place. His HP Model 5830A Double Column Mass Chromatograph pinpointed the material, but our girl Marissa (er, Marisa Tomei, the other Marisa!) had the automotive expertise to know which cars could or could not actually leave those tracks. It’s pretty much the same way with analyzing PCB corrosion. Any lab dweeb can tell you he found chlorides or fluorides in your crud; no great feat there. You need experts who know enough about PCB manufacturing and service environments to help you find out why the corrosion is happening in the first place. So go to a lab with specialized expertise in PCBs and corrosion analysis, and they will help you “track” down the source of your problem.5. Correct answer: False. Big time false! Fab and assembly chemicals are often the cause of PCB corrosion. Tulkoff tells us that PCB fabrication process is one of the most common sources of contaminants, as it uses the greatest amount of aggressive chemicals--chlorides, sulfuric and hydrochloric acids, methylene chloride, and a whole long list of things we never heard of and can’t pronounce. Kyzen’s Jack Reinke explains that organic acid fluxes, often referred to as “water wash” fluxes, are a common culprit. Organic acids are active metal reducers at room temperature. All they need to get them going is an electrical bias and a little water, which they conveniently pull from the atmosphere. If they are not properly cleaned, they will definitely eat your board. Don’t let the term “no-clean” fool you into thinking that these types of fluxes are safe and reliable under all conditions. “No-clean” is really just shorthand for “don’t have to clean most of the time for most electronic assemblies in most applications.” If a no-clean flux is not properly activated with enough heat during soldering, or if it’s operating in a moist environment, or if it was only partially cleaned, or if the circuit board has high voltage differentials, watch out! That’s a lot of "ifs" to watch out for, which is why more and more companies are cleaning their no-clean assemblies with specially designed solvents.
6. Correct answer: False. IPC standards exist for PCB cleanliness, but not for assembly cleanliness (just a bit of a trick question). IPC-5701, -5702, -5703, and -5704 all address PCB cleanliness, but no standards exist for post-soldering cleanliness. J-STD-001 does mandate a cleanliness level of 10 ug/in2 for assemblies manufactured with ROL0 or ROL1 flux if cleanliness testing is performed, but it’s not required unless specified by the customer. Whaddaya know, another if! 7. Correct answer: True. The best way to make sure the flux residues don’t affect the circuit performance is to remove them completely; duh. But completely is the key word. Water wash fluxes used to be called “water soluble,” but most modern ones require some type of chemistry to facilitate the cleaning process; hence the subtle change in nomenclature in recent years. No-cleans fluxes always need solvents to dissolve their resins, and leaving a little behind is far worse than not cleaning them at all. Regardless of flux type, removing all of the residue from underneath low-standoff components like microBGAs and QFNs is about as tricky as winning a limbo contest after a few margaritas. If you are trying to clean under these, you need to check with your cleaning equipment manufacturer and your chemistry supplier to make sure you are using the most effective technologies, and then get your process validated by a lab that can pull the parts off the PCB and analyze what lies beneath them. 8. Correct answer: True. The best way to make sure that corrosive gasses, moisture, salt air, or other environmental risk factors don’t affect your circuit performance is to keep them off your PCB. Conformal coating puts a barrier between the circuit and the environment. If you want to practice “safe circuitry," choose your barrier wisely. The exact kind of coating that works best depends on the kind of environment your circuit board is going into. Tulkoff warns that, “While coatings offer some protection, traditional conformal coatings are NOT hermetic. Moisture will diffuse through, and they require good adhesion to the circuit board to perform properly. Even tiny areas of voids, bubbles, or delamination will drive micro-condensation and can raise the odds of ECM by concentrating the contamination that the coating is trying to protect against.” She also provided Figures 5-7, which show coating defects and corrosion underneath and on top of conformal coatings. Yet more and more reasons why cleanliness is so critical!
Figure 5: Voids and bubbles in conformal coating.
Figure 6: Sulfur (creep) corrosion under conformal coating.
Figure 7: Dendritic growth OVER conformal coating. 9. Correct answer: any choice is correct. It depends on the application. Nordson Asymtek’s Jerry Frost draws on his 25+ years of conformal coating experience to advise us about specific classes of materials usually recommended for certain operating environments:
- Urethanes protect against chemicals, salt fog, and moisture;
- Silicones are the best choice for hot and humid environments, as long as they’re not sufur-rich;
- Acrylics are used in environments that require moisture protection and potential rework;
- Epoxies are available for general purpose, but are not very popular; and
- Parylene is the gold standard in conformal coating. It is the most robust for protecting against almost anything, but it is also costly and slow to apply.
10. Correct answer: c or d. Subtract an extra point if you guessed b because it’s a really stupid answer. Most conformal coat materials have UV tracers in them to facilitate inspection, which is critical. Parks reminds us that it only takes one single bubble to precipitate failure. Figure 8 shows the blue glow of the coating under a black light. When viewed with UV-A illumination, bubbles or pinholes in the coatings are easy to spot. Additionally, new AOI algorithms are now available that can automatically inspect for conformal coating defects, presumably more accurately than humans can.
Figure 8: Conformal coating inspection under UV light.
Scoring
What’s your Corrosion IQ? Give yourself one point for every correct answer and deduct one point for every incorrect answer. And as a special geek bonus, give yourself an extra point if the terms “positraction” or “limited slip differential” popped into your head as you thought about My Cousin Vinnie.
If you scored 8-10: You are a corrosion expert. Congratulations! You’re an expert on corrosion and proud of it. Crust, rust, creep, or crud; you ”get” corrosion. We don’t mean you actually corrode; we mean you understand the phenomena (sorry, had to explain that for the negative scorers). Even better, you know that corrosion usually doesn’t rear its ugly head until after your instrument is out in the field where people rely on it to perform. So, like any good geek, you take precautions by making wise choices in assembly processes and proactively reducing your risk. Now show this to your boss and ask for a raise!
If you scored 0-6: You are a corrosive epert in training (EIT). You’re a little creepy and a little cruddy, but no real threat to the experts who outscored you. We suspect you scored well because every dork and his dog have seen corrosion when changing out the batteries in his electronic toys--like your radio-controlled trucks, electric scooters, pocket language translators, personal robots, flip phones…shall we go on? Didn’t think so. Too bad you didn’t know about the impact of the environment on your PCBAs or you would have taken better care of your toys so they didn’t corrode in the first place. But no worries; keep taking our quizzes and soon enough you will be an expert, and your toys will thank you.
If you scored less than zero: You are a loser. You’re the idiot who sees corrosion and says “throw some cola on it; it’ll clean up just fine.” Pleeeaaase!! Don’t even try to pretend you know what you are talking about, especially when it comes to circuit boards. Just keep quiet so your career doesn’t become a humorous war story of really epic, spectacular failures. And get your geek on: Keep taking the quizzes and learning about PCBAs, and maybe someday you’ll reach EIT status.
Many, many thanks to the experts who helped answer our critical corrosion questions: Bill Parks, Jack Reinke, Jerry Frost, Randy Schueller, and a very special shout out to Cheryl Tulkoff for all the fantastic information and the way cool pictures--she’s the honorary PCB Girl-Geek of the month!
More Columns from Various Archived Columns
Slash Sheet Chaos: Is What You See, What You Get?Moisture in Materials: Avoiding Process Gremlins
Material Witness: Beat the Heat--A Non-Math Intro to Thermal Properties
Material Witness: Considerations in Using TC Materials for PWBs
Material Witness: Are Your Materials Up to the Challenge?
Material Witness: Thermal Oxidation of Materials, Part I
Material Witness: Thermal Oxidation of Materials, Part II
Material Witness: R.I.P. Speedboard C